Stucco is a highly specialized and skilled process, so it’s important to work with a professional. A stucco contractor will inspect the home to ensure the sheathing and framing are strong enough to support the stucco and eliminate any existing cracks.
The process of applying stucco involves a three-coat system. The first layer is an asphalt-infused paper, followed by a layer of furred chicken wire and then the scratch coat. Contact Dryvit Stucco Installation now!
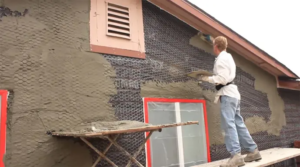
Before applying stucco, the walls must be cleaned and primed with a bonding agent. In addition, any existing cracks or damage to the walls need to be repaired. This will ensure that the new stucco adheres properly and prevent any underlying issues from exacerbating over time. For example, hairline cracks may allow water to leak between the internal wall and the exterior layer, resulting in mildew or mold. This can also lead to structural issues, so it is important that these cracks are repaired before proceeding with the installation. In some cases, this might mean repairing the cracks with high-quality acrylic caulking or elastomeric sealants or using more extensive patching techniques for larger areas. It is also a good idea to protect the walls against moisture penetration by applying a moisture barrier, such as a stucco wrap or a liquid-applied waterproofing coating.
Once the surface is prepared, it is ready for the first coat of stucco, known as the scratch coat. This coat is made of a mixture of cement and sand and is applied evenly with a trowel. It is then scraped to create horizontal grooves, which will provide a strong base for the brown coat and subsequent layers of stucco.
It is recommended that the scratch coat be left to cure for at least a day. While this is not always possible, it will ensure that the stucco adheres to the lath and reduces the chance of future issues.
When the scratch coat is finished curing, it can be painted if desired. This can add a nice aesthetic to the finished project. Additionally, it can help to hide any imperfections in the lathing and the scratch coat.
Lathing
Often the focus of new stucco projects is on colors, textures and finishes. However, these only serve to highlight the overall importance of a complete cladding system that includes weather barriers, flashings and control joints. It is these structural elements that prevent moisture intrusion to the framing of your house and minimize cracking once the plaster has cured.
To begin the lathing process, the old sheathing or other existing covering will be removed to expose the studs and framing members of your home. Next, the studs, headers, and framing members will be inspected and replaced as needed. This is done to ensure that they are strong and sturdy enough to support the weight of the plaster and withstand any water penetration or other moisture intrusion.
There are several options for the lathing stage including weep screeds, asphalt coated waterproofing paper and lath wire (also known as chicken wire). The type of lath used is largely dependent on the scale of your project and the surface onto which the stucco will be applied. Metal lath tends to be the preferred option for larger projects with more structural demands, while fiber lath is a popular choice for do-it-yourself applications.
Lath wire comes in a few different styles and gauges but typically a 17-gauge hexagonal furred pattern is used to create a stronger more durable structure for the stucco to grab onto. Whether the lath is welded together or nailed in place, nail patterns vary as well. Dog ear nails, for instance, are used on older homes with welded wire lath but are not recommended for modern applications as the furred edges of the nails can cause rust and damage to your plaster.
Scratch Coat
The scratch coat is the first of the three layers that make up a stucco system. It is a base coat of field-mixed Portland cement, sand, lime and water. It’sIt’s typically applied at a depth of around 3/8 inch. A tool called a scratcher is used to make horizontal lines in the mixture, which gives it a rough surface and provides a mechanical bond. In addition, a few of the ingredients in the scratch coat can help facilitate chemical bonding with layers that come later.
The mix for this coat can vary a bit, but a good rule of thumb is a 3 part sand to one part cement ratio. Lime is also usually included, which helps the mix stick to the walls. Other additives can also be used, but they are not always necessary.
This layer is a critical step in the process, and it’s important that it is done right. Not only does it provide a strong foundation for the rest of the base coats, but it it’s also crucial to the durability and longevity of your home.
A professional stucco company will know the best way to apply this coat. It can be applied by a hawk and trowel, or sprayed on. After the scratch coat is sprayed or poured, it’s allowed to dry and cure for a few days.
During this time, it’sit’s imperative to protect the product with a tarp and avoid water or other weather that may interfere with the curing process.
Brown Coat
The brown coat is the second base layer that goes over the scratch and helps even out the walls before the finish stucco is applied. It is troweled smoother than the scratch coat and covers all lath and corner aids completely. It also adds thickness to the stucco system and provides a base for the final color coat to adhere to.
While it’sit’s not the most exciting part of a plaster job, the brown coat is critical to achieving superior finishes. If a plasterer doesn’tdoesn’t spend the time to properly prepare this layer, it will be difficult to achieve the desired texture for the finish layer.
This is why it’s essential that contractors give themselves adequate time for the brown coat to dry. This will ensure that it is ready for the poly prep and color coat to be applied. A good rule of thumb is to allow at least 24 hours for the brown coat to cure. However, consult with your specific product for the exact amount of time needed.
Using a variety of tools, contractors can apply the brown coat in different ways to create a number of unique textures. Each technique offers a unique set of advantages for the finished project.
The three coat stucco system has been around for over 100 years and continues to be a popular cladding choice for commercial, multi-family and residential projects. This is due to its many benefits including durable, attractive and energy efficient cladding.
In areas prone to wildfires, the three-coat stucco system is a fortress for homes and provides formidable fire resistance along with visual appeal. This unmatched combination of durability and beauty is what sets the system apart from other cladding choices.
Finish Coat
When it comes to exterior wall finishing, stucco is a durable and attractive material. It’sIt’s available in a wide range of colors and textures, with the ability to incorporate stone or glass chips into the mix. Modern stucco includes added polymers for increased flexibility, making it more resistant to cracking.
A stucco finish requires regular maintenance to prevent excessive water penetration and a breakdown of the material. It’sIt’s important to keep the stucco clean, repairing any cracks as soon as they appear and re-watering frequently. Stucco is a versatile and appealing option for any home, whether it’sit’s traditional or modern in style.
Stucco is also an excellent choice for homes in arid climates. Its 1-inch layer offers a one-hour fire rating, protecting the house from heat and flames. It can also be used as a decorative accent to existing structures, such as stone walls and reclaimed bricks.
While it is possible to perform a do-it-yourself stucco application, it’sit’s always best to hire a professional for the job. Reputable contractors will ensure the work is done properly, preventing costly repair later. They can also offer warranties and insurance to protect homeowners against any damage during the project.
For those interested in saving time, money and labor, the one coat method of stucco is growing in popularity. It is a simpler process than the three-coat method, but still provides the same benefits of durability, design flexibility and impressive fire resistance.